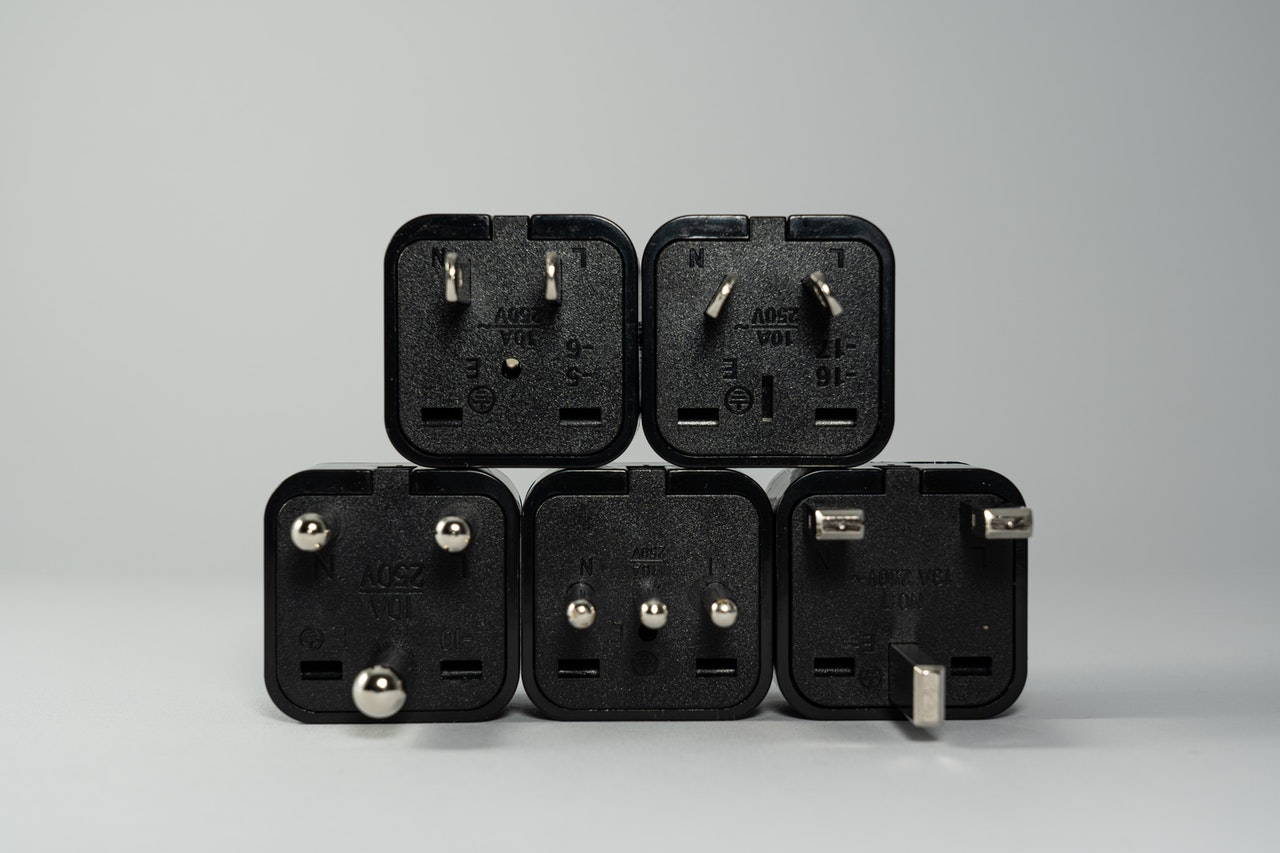
高温线电子设备带来设计和可靠性挑战(2)_高温线
使用超出数据表温度规格的 IC
过去,高温线电子设计人员,例如石油和天然气行业的设计人员,由于无法获得高温 IC,被迫使用远高于其额定规格的标准温度组件。一些标准温度 IC 确实可以在高温下工作,但使用它们是一项艰巨且冒险的尝试。例如,工程师必须识别潜在的候选者,全面测试和表征随温度变化的性能,并在很长一段时间内验证部件的可靠性。零件的性能和寿命通常会大幅降低。这是一个具有挑战性、昂贵且耗时的过程:
- 合格的组件需要在带有高温印刷电路板 (PCB) 和固定装置的实验室烤箱中进行测试,时间至少与任务要求一样长。由于可能会遇到新的故障机制,因此很难加速测试。测试期间的失败需要再次迭代组件选择和长期测试,从而延迟项目时间表。
- 不保证超出数据表规范的操作,并且组件批次之间的性能可能会有所不同。特别是,IC 工艺变化可能会在极端温度下导致意外故障。
- 塑料封装仅在高达 175°C 左右的温度下仍能保持稳健——使用寿命会缩短。在这个温度极限附近,如果不进行昂贵且耗时的实验室故障分析,就很难区分封装相关故障和硅相关故障。陶瓷封装中的标准组件很少见。
- 通常,在恶劣环境中使用的组件不仅要承受高温,还要承受剧烈的冲击和振动。许多工程师更喜欢使用带引线的封装,例如 DIP 或鸥翼 SMT,因为它们为 PCB 提供了更坚固的连接。这进一步限制了器件的选择,因为其他行业趋向于更小、无铅封装。
- 可能希望获得模具形式的零件,特别是如果一个组件只能在塑料封装中获得。然后可以将管芯重新封装在符合高温要求的密封封装或多芯片模块中。然而,在少数可以在高温下工作的组件中,有一小部分组件可以作为测试芯片轻松获得。
- 由于时间限制和测试设备的限制,行业工程师可能倾向于将设备的鉴定限制在特定的应用电路中,而不涵盖所有关键设备参数,从而限制了其他项目的组件重复使用而无需进一步测试。
- 关键的非数据表 IC 特性,例如金属互连中的电迁移,可能导致高温下的故障。
专为高温设计并符合要求的 IC
幸运的是,最近的 IC 技术已经生产出可以在高温下可靠运行的器件,并具有有保证的数据表规格。在工艺技术、电路设计和布局技术方面取得了进展。
管理许多关键设备特性对于在高温下成功、高性能运行至关重要。最重要和众所周知的挑战之一是衬底漏电流增加。其他一些是载流子迁移率降低、器件参数(例如V T、β 和V SAT )的变化、金属互连的电迁移增加以及介电击穿强度降低。6虽然标准硅的工作温度远高于 125°C 的军用要求,但7每升高 10°C,标准硅工艺中的泄漏量就会增加一倍,这对于许多精密应用来说是不可接受的。
沟槽隔离、绝缘体上硅(SOI) 和标准硅工艺的其他变体大大降低了泄漏,并使高性能工作温度远高于 200°C。图 5 说明了 SOI 双极工艺如何减少泄漏面积。宽带隙材料,如碳化硅 (SiC),将标准提高得更高;在实验室研究中,碳化硅 IC 的工作温度高达 600°C。然而,碳化硅是一种新兴的工艺技术,目前只有功率开关等简单的器件可商用。
仪表放大器:仪表放大器在井下钻井应用中需要高精度,以在通常存在的嘈杂环境中放大非常微弱的信号。这种特殊放大器类型通常是测量前端的第一个组件,因此其性能对整个信号链的性能至关重要。
ADI 开发团队从一开始就将AD8229仪表放大器用于高温操作,并为此从头开始设计。为了满足其独特的性能要求,专有的 SOI 双极工艺是首选技术。设计人员实施了特殊的电路技术,以保证在各种器件参数(例如基射极电压和正向电流增益)下工作。
IC 布局也严重影响 AD8229 的性能和可靠性。为了在整个温度范围内保持低失调和高 CMRR,布局补偿了互连和温度系数的变化。此外,仔细分析关键部分的电流密度减轻了电迁移的影响,有助于提高极端条件下的可靠性。同样,设计人员预测故障条件以防止过早击穿。
稳健的工艺、电路设计和布局技术相结合,使器件能够满足温度范围内最严格的精度和可靠性要求。
包装注意事项
一旦高温功能性硅在手,这场战斗只赢了一半。封装芯片,然后将封装连接到 PCB,在高温下并非易事。许多因素会影响温度下的封装完整性(图 6)。
芯片连接材料将硅固定到封装或基板上。许多经证明可在标准温度范围内使用的材料具有较低的玻璃化转变温度 ( T G ),不适合高温操作。需要特别注意匹配裸片、裸片连接和衬底之间的热膨胀系数(CTE),以使裸片在宽温度跨度的循环中不会受到应力或破裂。即使是芯片上的轻微机械应力也会导致电气参数转变到精密应用无法接受的水平。对于需要与封装基板进行热连接和电连接的功率器件,可能需要金属芯片连接材料。
引线键合是一种通过将金属线从引线框架连接到管芯表面上的键合焊盘来将管芯互连到引脚的方法。当考虑高温下的引线键合可靠性时,用于引线和键合焊盘金属化的金属的兼容性是主要问题。与键合金属相容性差有关的故障有两个方面:在边界界面处金属间化合物(IMC) 生长,这会产生脆性键合;和扩散(柯肯达尔效应),它会在界面处产生空隙,削弱粘合强度并增加其电阻。不幸的是,工业中最流行的金属组合之一——金线和铝焊盘金属化——在高温下容易出现这些现象。图 7 是 Au/Al 键的剖面图,显示了 IMC 生长,这会在高温下 500 小时后损害键的完整性。
图 8 显示了在高温下键合失效后大量的 Au/Al 金属间化合物生长和 Kirkendall 空洞。更糟糕的是,溴和氯等卤素(有时存在于模塑料中)会在高温下导致边界界面腐蚀,从而加快失效时间(尽管幸运的是,该行业正在转向“绿色”无卤素模塑化合物)。因此,有强烈的动机将相同的金属用于键合线和键合焊盘(单金属键合)以避免这些负面影响。如果这是不可能的,工程师应该选择具有足够慢的 IMC 增长和扩散速率的金属,以便在所需的使用寿命内保持可靠。
还必须评估封装引线配置和金属化。表面贴装元件仅取决于铜层和预浸渍材料(预浸料)之间的焊盘面积和粘合剂的质量。另一方面,通孔 DIP 配置是业界最成熟和最可靠的封装之一,也提供强大的冲击和振动性能。在极端情况下,可以通过弯曲电路板底部的引脚以将其“钉”到 PCB 上来进一步提高连接强度,但通孔引脚排列不允许组件填充电路板的底部 – 这可能是主要的关注空间有限的井下仪器等应用。
在许多情况下,鸥翼 SMT 引线配置是一种可行的替代方案,但在许多高温环境中遇到的高冲击和振动条件下,无引线 SMT 可能不够坚固。使用 SMT 组件时,设计人员应考虑其高度和质量。高温环氧树脂的应用将提高附件的坚固性,但会增加制造成本并限制进行维修的能力。在所有情况下,铅金属化必须与高温焊料兼容。
最流行的标准焊料合金的熔点低于 200°C。然而,有一些现成的合金属于“高熔点”(HMP)类别,熔点远高于 250°C。即使在这种情况下,任何承受应力的焊料的最高推荐工作温度也应低于其熔点约 40°C。例如,5% 锡、93.5% 铅和 1.5% 银的标准 HMP 焊料合金成分的熔点为 294°C,但建议仅在最高约 255°C 的温度下使用。9请注意,BGA(球栅阵列)封装的焊球由工厂附接,其熔点可能不高。
最后,PCB 本身是潜在的故障源。标准 FR4 的玻璃化转变温度范围为 130°C 至 180°C,具体取决于具体成分。如果在高于此温度的情况下使用——即使持续时间很短——它也会膨胀和分层。一种经过验证的良好替代品是聚酰亚胺,它与 Kapton 中使用的材料相同,其T G高达 250°C,具体取决于成分。然而,聚酰亚胺具有非常高的吸湿性,可通过多种机制迅速导致 PCB 失效,因此控制水分暴露非常重要。近年来,工业界推出了吸收较少水分并在高温下保持完整性的特殊层压板。
本文由程达电器原创分享
官网由宁波久五网络有限公司设计制作